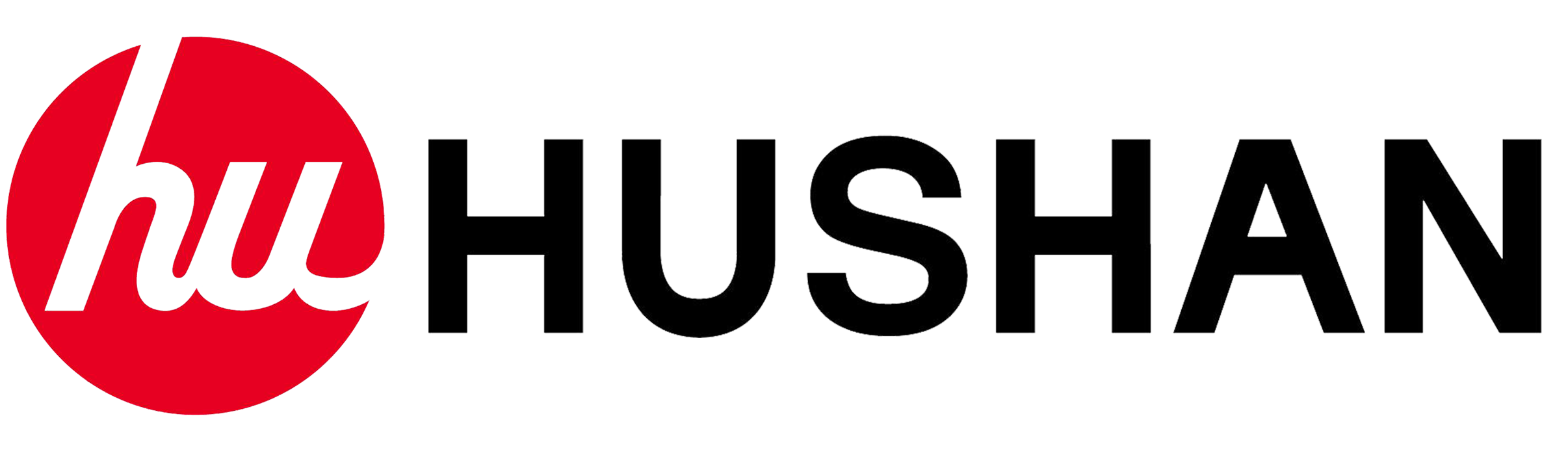
- 客户: 虎山实业股份有限公司
- 产业: 汽车
- 解决方案: Moldex3D eDesign
大纲
虎山实业一直苦于无法解决缝合线问题,对于缝合线带来的质量影响束手无策。希望藉由应用Moldex3D模流分析软件找出缝合线分布,用不同的设计变更组合找出消除缝合线的方法,以及验证设计变更的可行性。
挑战
产品末端出现明显缝合线 (如下图所示),而虎山这类的把手案件非常多,模具厂告诉他们不论如何修改模具都无法避免结合线出现在外观面。希望透过模流分析验证模具厂的想法是否正确,更希望透过解析原理,进而找出合适的设计方式,并解决缝合线问题。
解决方案
利用Moldex3D eDesign方案快速建立真实三维网格模型,协助虎山实业能够针对浇口位置及产品厚度自由进行设计变更,让设计符合产品实际生产需求,却无需耗费实际试模和修模费用,不但成功化解恼人的缝合线问题,更能兼顾产品质量与成本。
效益
除了调整产品厚度之外,改善产品缝合线位置的方法还可以从更改浇口位置着手,以此原则使用CAE软件共进行了46组设计变更,从中选定最佳几何设计进行修模。以小型产品为例,修整模具约5~10万进行估算,一组模具需要50~100万不等。由此结果计算,可以免去进行其他45组设计的修模或开模费用,省下的成本十分可观。
案例分析
虎山实业欲进行修改的模型为车门内门把,此产品以单浇口进行射出成型时,机构设计出现缝合线。车门门把因使用次数频繁,且为外观件,产品的外观及耐用度要求都很高;若门把出现缝合线,成型后产品的强度及外观上都会受到影响。由于此产品已开模生产,生产时却发现产品末端出现明显的缝合线,因此希望能藉由模流分析,以低成本及低修改幅度为前提,降低模型缝合线的可见度及长度,避免缝合线问题影响产品外观及强度。
图一中为产品设计,图二中为产品之厚度分布图。由图二中可知,产品原始肉厚设计为均一厚度,未出现厚度差。
由图三中可知熔胶于不同充填时间下的流动波前位置,图四中表现出原始产品设计下,出现缝合线位置和其充填时间,由此可知缝合线交会角度及出现缝合线长度。
由图五中可知,原始设计下流动结果呈现出之缝合线长度约9.5 mm,会合角度为约90°。
图五 原始产品设计缝合线长度及会合角度
波前接触的角度视为缝合线出现与否的重要参考依据。根据熔胶接触的角度开始计算缝合线的长度,由判定的结果来看,熔胶波前夹角在大于90°或135°以上,可以视为分子排列方向近乎一致,不会再有缝合线产生。
经多组浇口或产品肉厚设计变更测试后,最终决议之设计变更如下方图中所示,以下一一进行说明。
厚度设计变更:
将孔洞处厚度加厚,平面中心位置减薄,引导波前于孔洞周围流动较快速,使两波前交会于边缘位置,交会角度较大且长度较短,可得长度较短之缝合线。
厚度变化斜角设计:
利用斜切设计使厚度产生变化,目的为引导流动波前于孔洞周围位置流动较快,外围则可流动较缓,藉此使波前交会位置为缝合线影响较小位置,且交会长度较短。
圆柱设计变更:
将波前交会位置附近圆柱设计更改为空心柱,减少熔胶充填入之体积量,使左方之流动波前不因圆柱设计而出现流动迟缓状态。
经设计变更后流动波前结果如下图中所示:
图十二 设计变更后缝合线长度及会合角度
此产品经过整体结构设变及浇口位置变更后,从仿真结果发现,藉由降低产品厚度及结构角度改变熔胶波前,进而修正结合线会合角,成为最佳设计变更方案。
原始设计中的产品面缝合线长度为约9.5 mm,经由设变后缩短近50%,缩短至 4.3 mm。
此项目一共进行了46次设计变更,终于找出这类车门把手的缝合线规则,并了解形成的原因。若以传统试误法进行,一定无法将心中的疑惑落实成科学化的数据,只能受限于模具厂而无法将技术能力厚植在自身的技术能量中。
藉由Moldex3D模流分析进行设计变更并选择设变中的最佳几何设计,可省去未来不着头绪的修模和试模,大幅减少成本支出。