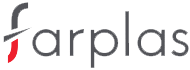
- 客户:FARPLAS A.S.
- 国家:土耳其
- 产业:汽车
- 解决方案:Moldex3D eDesign / Moldex3D MCM Module
大纲
本案例中的产品为油箱外壳,使用PP+GF30与乙烯丙烯橡胶(EPDM)两种塑料,经由多材质射出成型制程生产。多材质射出制程的难度特别高,玻璃纤维排向必须与流动方向一致,而流动方向将影响到产品是否变形。若产品扭曲的部位无法准确嵌入另一个腔室,EPDM将无法成功充填。此外,要将EPDM完全平衡地填入分层精细的PP+GF30中,也是另一个难题。FARPLAS利用Moldex3D对油箱外壳的制程进行各项分析,最后成功预测出潜在的问题,并省下重复修模的时间。
挑战
- PP+GF30充填完成后产生的变形问题
- 对EPDM充填的进浇位置和产品局部厚度做出最佳设计
- 需要充足的EPDM充填量,以补满热浇道间隙
解决方案
Moldex3D可帮助FARPLAS获取正确的设计变更信息,协助改善第一次充填(PP+GF30)发生的翘曲问题,以及第二次充填(EPDM)的流动平衡和短射问题。透过高阶网格模拟,可得到极为精准的分析结果,与实验结果几乎是100%吻合。
效益
产品质量改善:
- 降低PP+GF30充填的总位移量
- EPDM充填达到零短射
- 节省设计修正的时间、缩短生产周期,并降低研发成本
案例研究
本案例目的为解决PP+GF30与EPDM多材质射出成型的翘曲问题。翘曲情形主要发生在第一次充填(PP+GF30)时,因此须针对此阶段进行改善,避免其成品无法与第二次充填(EPDM)的组件互相嵌合。同时第二次充填时的模穴,也须有适当的设计,确保充填完整。
FARPLAS首先利用Moldex3D进行第一次充填的模拟,分析结果预测出翘曲问题,于是根据模拟结果进行模具设计,并同步进行第二次充填模拟。FARPLAS针对第一次充填进行的修正包括:在部分区域增加肋条设计作为支撑,以强化产品坚固性;部分区域则移除肋条,使产品厚度较平均(图一)。经上述变更后,翘曲问题获得明显改善(图二)。
![]() |
![]() |
图一 与原始设计(左)相比,变更后的设计肋条增加了,并移除部分区域的肋条
![]() |
![]() |
图二 原始设计(左)缺乏支撑的肋条,翘曲变形较严重(最大值为2.78mm),变更后的设计(右)多了支撑肋条,
翘曲情形改善(最大值为2.47mm)
在第二次充填的部分,Moldex3D侦测出充填不完整而导致短射的现象。因此FARPLAS针对第二次充填进行产品几何(图三)和厚度(图四)的修正,改善了EPDM的流动行为,使充填完整,并成功解决了短射问题。
![]() |
![]() |
图三 第二次充填组件的原始设计(左)经过几何的变更(右)
![]() |
![]() |
图四 左图为EPDM充填组件原始设计,经设计变更后(右图)局部厚度增加
![]() |
![]() |
图五 原始设计(左)的短射问题经设计变更后(右)已获得解决
除了从分析结果看出设计变更后,翘曲和短射问题都获得改善之外,FARPLAS也以实验验证模拟的准确性。实验结果发现,将模流分析的网格等级从3提高到5之后,结果几乎是100%准确。图六及图七分别为EPDM充填的原始设计和设计变更比较,皆可发现模流分析和实验结果相符合。
![]() |
![]() |
图六 原始设计的短射位置,模流分析(左)与实验(右)呈现一样的结果
![]() |
![]() |
图七 设计变更后解决短射问题,模流分析(左)与实验结果(右) 呈现一样的结果
结果
经由Moldex3D网格等级5的模流分析,可清楚了解多材质射出制程中,PP+GF30和EPDM两次充填的流动行为,并藉由实验验证其准确度几乎达100%。Moldex3D帮助FARPLAS在实际生产前,提前预测潜在的制造难题,并及早做出必要的修正,避免耗费过多的时间成本在重复试模。