客户简介

- 客户:KOPLA Engineering
- 国家:韩国
- 产业:汽车
- 解决方案: Moldex3D eDesign / FEA Interface
大纲
本案例产品为一车门模块,原始产品有严重翘曲问题(图一),并因此导致组装上的困难。为解决此问题,KOPLA以Moldex3D模拟以塑代钢后的材料性质差异,并藉由Moldex3D FEA Interface进行结构分析(本案例结合ANSYS)。最后KOPLA得以藉此达到优化的浇口位置设计、决定适合的材料,降低翘曲并成功解决装配问题。
图一 本案例的车门模块有严重翘曲问题
挑战
- 严重翘曲问题
- 装配品质差
- 须达到轻量化目标
解决方案
KOPLA以Moldex3D eDesign及FEA Interface验证材料性质,并解决翘曲难题。
效益
- 成功改善翘曲
- 无缝整合模流和结构分析的工作流程
- 成功验证材料属性
- 降低试模成本
案例研究
本案例产品为一车门模块,由于组装需求,产品上有许多孔洞设计,因此孔洞的位置相当重要。本案例的最主要目的为改善产品翘曲问题,确保组装成功。
KOPLA决定以Moldex3D来寻找解决方法。首先必须找到适当的浇口位置,确保良好的流动行为和降低潜在的翘曲问题。KOPLA根据Moldex3D翘曲模拟结果,多次变更浇口位置,直到找到最佳的位置和浇口型态。
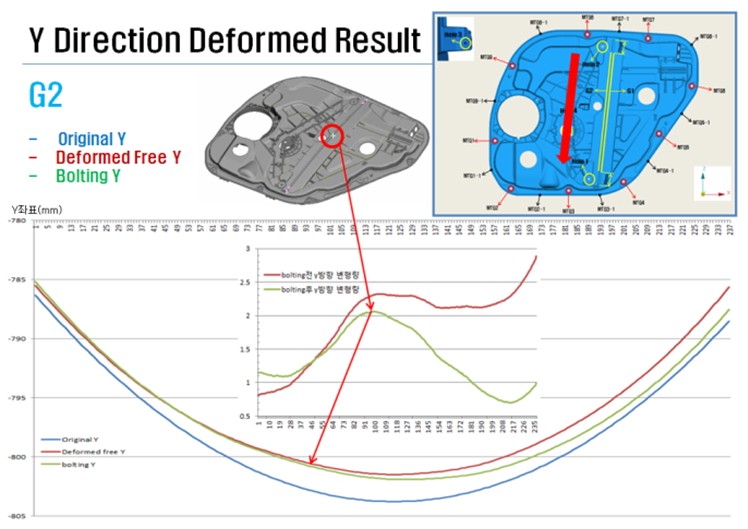
图二 KOPLA不断变更浇口位置设定,并个别进行翘曲变形的模拟
决定浇口位置后,KOPLA利用Moldex3D FEA Interface将翘曲的模拟结果,包括纤维配向、元素计算结果输出至ANSYS进行结构分析,以观察产品组装后的强度和稳定性。
由仿真结果发现,产品的平整面发生翘曲,而利用模具反变形可以补偿位移带来的组装问题,因此组装的孔洞位置将与预期相同。而在改变边界条件设定并检查装配组件的位移情形后,KOPLA成功改善变形问题,并提高产品结构强度。
图三 仿真变形产品的孔洞位置与预期相同
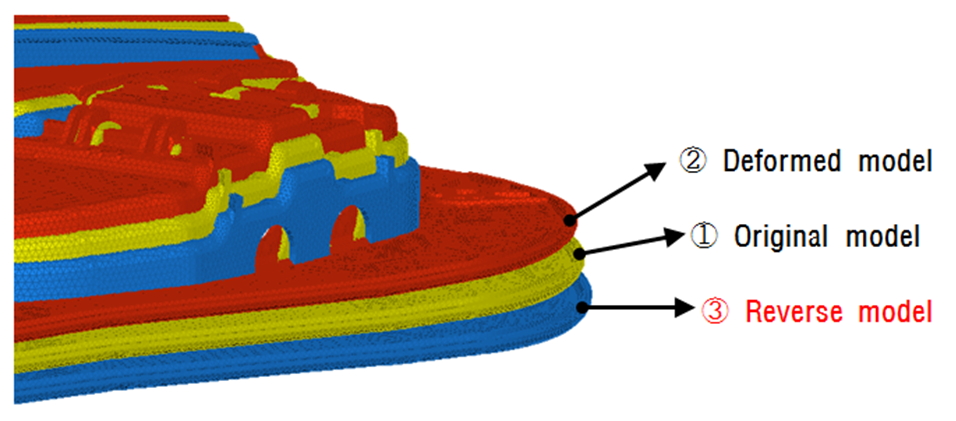
图四 本案例产品与其他组件装配时的结构分析结果
结果
透过整合Moldex3D与ANSYS,并验证仿真结果与实际制造结果高度相符,KOPLA成功改善了产品的变形问题及结构设计,且更能有效地掌握材料的属性,达成设计优化。